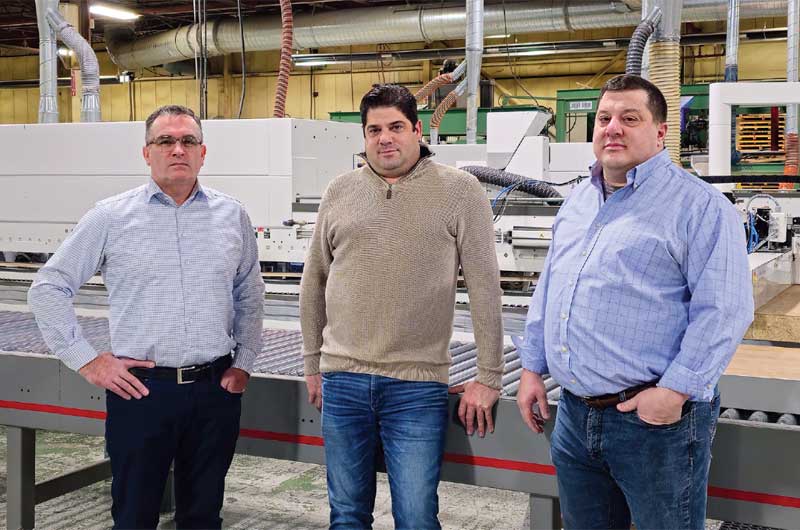
Photos: Contributed
The team at Think Lightweight, from left Ian McPhail, general manager, Evan Prince, senior projects director and Vern Prince, operations manager.
Think Lightweight Corp., a division of Cedarcrest Wood Products of Tillsonburg, Ontario is an expert in lightweight panel technology solutions and with more than 38 years of experience, “the company offers a full turnkey service for product design, product approval and volume production of lightweight panel technology.”
Not only does Think Lightweight manufacture lightweight products for the office furniture, retail, architectural, acoustic, hospitality and trade show markets, but they also constantly innovate by designing and prototyping new, leading edge products and solutions.
The company got its start as Cedarcrest Wood Products
in 1986, mainly as a cabinet shop, but general manager and CEO Ian McPhail said they transitioned to lightweight products and formed Think Lightweight Corp as a division of Cedar Crest Wood Products in 2015, because they saw a real need for innovation and new solutions for the sector.
“Since the early ‘90’s we were hired by a honeycomb manufacturer down the road from us to do some prototyping and product testing for their customer projects,” he says.
“And we ended up actually manufacturing lightweight products for their customers as the projects developed.”
They did that for a few years, and when that company was purchased and their business model changed, rather than stop manufacturing lightweight products, McPhail says they decided to continue because they firmly believed there was an important niche market for these kinds of products.
“So we continued to develop and expand that part of our business. We started sourcing core from other suppliers and continued manufacturing lightweight solutions for the industry and over time focused all of our efforts to primarily manufacture lightweight panels for our customers.
“I remember it very vividly, some of our early orders were for just 20 or 30 panels for office dividers. Today we do up to 2,000 lightweight panels per day. We have an automatic lightweight panel sizing line with robotic stacking and it sizes and stacks a panel every 16 seconds.”
CabinetmakerIan McPhail started his career in the industry as a cabinetmaker providing millwork to the commercial and healthcare industries.
Born and raised in Toronto he entered the apprenticeship program completing schooling at George Brown College, when McPhail’s parents moved to Woodstock he decided to move there as well.
He started at Cedarcrest Wood Products in 1993, as a cabinetmaker. At the time it was a 2,500 sq. ft. shop with four employees. In 1994, he joined their sales team and then in 2000 the ownership team. McPhail became general manager and CEO in 2019.
“Although I am the company principal, I have two key essential partners, Vern and Evan Prince, who are the sons of the original owner,” he says.
Today, Think Lightweight has fully transitioned to manufacturing lightweight products, everything from standard panels to highly customized
pieces for special applications.
“We are a premium lightweight component provider to the woodworking fabrication industry,” McPhail says.
“We do everything from divider panels to architectural panels for walls and ceilings as well as retail store components and thicker gables and shelves as well as special solutions for hotel rooms,” he says.
“So there are very varied applications for our products. Another big one for us is a door. We provide a significant volume of doors for fabricators for everything from multi-family dwellings to hotels and commercials applications.
“Trade show panels are also making a comeback and we manufacture wall-system panels.
“And during COVID-19 we pivoted and added an isolation cubicle program for one of our customers who transitioned to manufacturing isolation cubicles and cubicles for vaccine administration sites.”
Lightweight advantage “In addition to being lightweight, our products have the added benefit of using less materials as well as offering a better strength to weight ratio.
“We can span a lot farther with our products because traditional materials will sag just from their own weight and ours will not.
“And you can also reduce the amount of hardware needed for installations, because it is lighter, which also saves you money. And then obviously there is also ease of handling and it allows for more creativity, which is a big one for designers. Lightweight’s products are also more stable and consistent then traditional products
and transportation costs are lower as well.
“Let’s say you are trying to do a two by eight ceiling beam a hundred feet long in a solid material, it wouldn’t stay straight. But ours does because a hollow-core panel is actually a structure and when it is assembled and finished it maintains its consistency.”
McPhail cites the example of a shelf they developed for a customer supplying Crate & Barrel. The company wanted a thick shelf, 16 inches wide by 84 inches long that could take 150 pounds level loaded with less than 1/8th deflection. So Think Lightweight designed one to the required specs, tested it and achieved the required results.
“And after we load tested it and took the load back after 48 hours, it bounced right back to straight. A traditional product would not do that, if it had sagged, it would have stayed that way.”
McPhail says he doesn’t really don’t know of many other manufacturers “who could provide our kind of products,” and it is that fact along with their efforts and investment into constantly improving their products that helps them keep their edge. That and the fact they are also continuously updating their shop and machinery.
Think Lightweight operates from an 80,000 sq. ft. shop with 54 employees.
They’re running two white glue press lines capable of up to 5x12 pressing (Black Brothers), two PUR press lines “and other than that we are pretty much a HOMAG shop,” McPhail says.
“We have three HOMAG CNCs with aggregate head for horizontal drilling and three HOMAG EDGETEQ edgebanders.
“And the newest one has a 100 mm capability, and that’s the first one in North America, that’s really exciting.”
McPhail says they added the 100 mm capability because architectural, tradeshow and retail market requests for volume components thicker than 2 ¼” drove their decision to invest in the 100 mm HOMAG edgebander.
“It allows us to strengthen and enhance our reputation as a leading edge lightweight panel manufacturer that produces volume projects economically.”
And he says they are grateful to Marco (Fernandes) and his team at HOMAG for “doing such an excellent job supporting us and helping us find the right solutions. We appreciate their support.”
Then there are three HOLZMA beam saws, two front load (one with automatic loading), and one with rear load. Also, three contour edgebanders, two from HOMAG and one SNX, as well as the aforementioned automatic lightweight panel sizing line with robotic stacking, which is a complete custom design they did in-house.
“And we don’t do any finishing,” he says.
“A lot of our products are laminated, edged and machined and we send them out raw or veneered if someone wants to do their own finishing.
“The thing is with finishing we’re often providing a component to go with other products and if you finish in two different plants with slightly different methods you get a different result, so in order to get the consistency needed its better if it is finished using the same process.”
Leading edge“One of our goals has always been to stay leading edge in product development and equipment. And when you do that you actually help drive design and it allows you to stay ahead of the competition,” McPhail says.
“We take a longer range view of products and design and customer relationship. We want to be able to drive developments.
One of those developments is a spin-off of their COVID isolation and vaccine cubicles. They have since transitioned that program into a product for homeless shelters and through their office furniture customers they have literally sold thousands of cubicles that are being used across North America.
“We are a premium lightweight panel component provider to the woodworking fabrication industry,” McPhail says, “and we have the capacity to economically manufacture edged and machined panels up to 3 ¾” thick in production volume.
And while they have the capability to produce up to 2,000 lightweight panels a day, he says they also do small, custom orders for small to mid-size shops.
“So we also manufacture an unfinished thick gable for fridge or double ovens. It’s been very popular because most of the time they are doubling up 5/8” MDF or ¾” MDF and then edge banding it, and it is really heavy, whereas our product is light weight, which means you are taking out up to 70 per cent of the weight.
“We have many large customers, but also many who just buy 20 at a time, enough for lower production.
“And because we started out with the office furniture industry, we’ve always had to be very flexible and that’s the other advantage we have, we inventory most of the lightweight product material and then we can fill large and small orders as needed.
“The idea is that we make it easy to buy a lightweight panel and as I said before, we are very committed to design and prototyping to make sure our product works for you. Many of the larger projects can take over a year and it’s a process. So we want to make sure we build the right product for you and that it works for you.
SustainabilityThink Lightweight has also gone for a global sustainability rating – EcoVadis is one of the world’s largest and most trusted provider of business sustainability ratings – and McPhail says they are quite proud of that. “It’s much more than ‘is your wood sustainably sourced,’ it applies to everything.
“A lightweight panel is saving 60-80 per cent of material before you even get started and all our offcuts are reused or recycled.
We are diverting around 90 per cent of our waste, some 600 metric tonnes annually, from landfill. So not only are we using a lot less material, but most of our waste is diverted to another use.”
McPhail says they’ve produced over 30 million sq. ft. of lightweight panels and by using lightweight technology their clients not only get easier and quicker installations, but they are also using a product that is more sustainable and stable than traditional materials.
“So thanks to our state-of-the-art materials and technology, we can deliver a better product that meets all your project requirements and at a lower cost.”