Two years ago, in my fifth column for Woodworking Magazine, I addressed how we as an industry need to change our culture to perform and compete globally as an industry. I spoke about the importance of industry collaboration and how industry-led cluster networks are contributing to the success of the 10 leading global GDP countries (Canada is #11).
It occurred to me that while we are moving forward, we still have a long way to go.
Companies in Canada and our governments are starting to learn about the value and power of cluster ecosystems to drive the economy. But how are other countries really doing it? What makes the companies in those countries different from us? Is it technology and automation? The latter certainly makes a big difference. But the biggest reason, is culture change within the industry.
Culture: Merriam-Webster dictionary offers a definition of culture that applies to industry and organizations: “The set of shared attitudes, values, goals, and practices that characterizes an institution or organization.” (Merriam-webster.com). From this definition, we can gather that a particular industry culture is determined by the behaviours of its members that reflect those “values, goals, and practices.”
Change: All of us who have studied organizational development or tried to implement change in our companies, such as lean manufacturing, quality systems or ERP, know that there must be buy-in from employees. Change, while facilitated strategically by management, also requires employee empowerment and ownership (bottom driven) to affect culture change to support the initiative(s). These are important premises to remember internally as we endeavour to make our companies successful.
What about outside of your company? What does culture change mean beyond the walls of your building and your processes? What behaviours enable “industry culture change”? What are the benefits and why should we bother?
Before we can address the above questions, we need to analyze who we are as the wood manufacturing industry here in Canada. Who are we really?
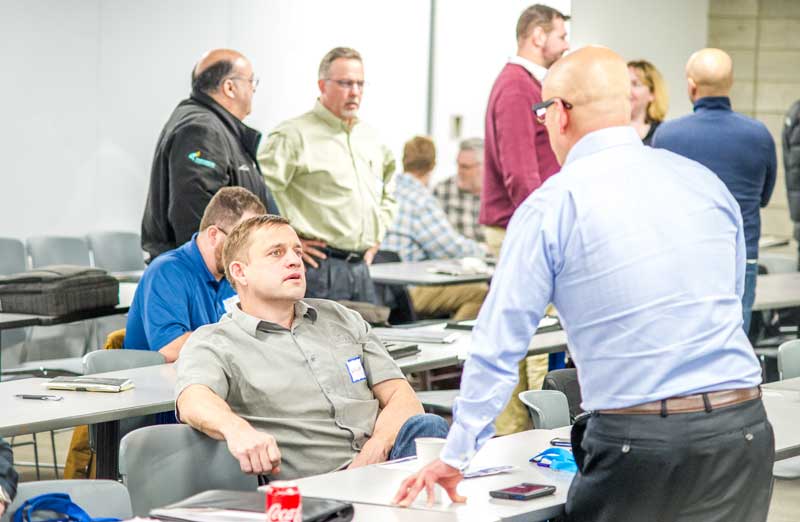
We are the secondary (manufacturing) wood industry. Our segments are many that include cabinetry, commercial millwork and fixtures, furniture, modular manufacturing, mass timber construction, flooring, wood components, and other niche wood products. Our industry for many years has been dominated (politically and otherwise) by the primary wood industry (sawmills, pulp and paper mills, primary product and bio-mass producers, and export of same). With Canada being traditionally a resource economy, provincial and federal governments have prioritized supporting the primary wood industry. Accordingly, secondary manufacturing, (that’s us) has gotten little or no attention over the years (although governments are now going through their own culture change as they learn to recognize us more).
As per North American business culture tradition, our secondary wood industry has been very competitive between companies within all the segments. We have been socialized to look out for the other guy who is doing the same thing and protect what you know and try to beat them. Some of us think we have trade secrets. (But most agree there aren’t really any real trade secrets in our industry sector). Some of us think that once we have established a certain level of market share and size, we know more than anyone else that is different. We think we have nothing to learn from someone who is smaller, or can’t relate to someone who is bigger, or different. We are trained to be suspicious and untrusting of others by nature. We build invisible walls and barriers. These behaviours are the cultural handcuffs that prevent the Canadian wood industry from thriving and reaching its potential.
My father entered the textile industry right after the Second World War and worked for over 40 years in that industry. When I told him about my work helping wood manufacturing companies learn from each other, he thought I was crazy. He, like many of our readers, didn’t know what an industry-led cluster was. He didn’t understand why companies would want to be collaborating at all, since they could potentially be competitors, and steal their ideas and customers. What he knows and understands is old thinking from his time. Once I explained how companies can get better and improve through collaborating together and learning from each others’ successes and failures, making the industry stronger, he totally understood it. For many, what comes next to facilitate “industry cultural change” are learned behaviours. For others, these behaviours I am about to discuss come naturally.
To change the culture of our industry as a whole, it has to come from individuals like you, and your employees. Culture change beyond our own companies means changing how we view others in our industry. It means looking at other companies and people, that typically could be construed as competitors or adversaries, as being comrades in arms, engaged with the same enemies and risks: loss of profits, loss of market share, production waste, quality challenges, increased costs, foreign competition, reliable supply chains, productive work force, health & safety, legislative compliance, taxes, new industry trends; the list goes on and I’m sure you could add to it.
These behaviours that enable “industry culture change” are the ones that require a new kind of thinking. It calls for behaviours that foster relationships with those you may not normally gravitate to or typically be guarded with. It involves some mutual risk taking, and reciprocity to establish trust. It calls for understanding that mutual challenges, along with mutual solutions, exist to be embraced and shared.
It also involves looking for common ground in other industries outside your specific segment of manufacturing, since many generic functions and best practices of manufacturing and business operations exist across all our wood segments listed above. (The programming the WMCO cluster delivers to our industry reflects these common business needs.)
It means that those of you who represent larger firms need to acknowledge that you still don’t now everything, or know more than the next company because you are bigger. The reverse is true for smaller companies, who may feel they have nothing in common with larger ones. This is outdated thinking. Acknowledging you have something to learn from everyone, that size doesn’t make you elitist in the industry, are examples of the behaviours that enable industry culture change. These behaviours are very common in industry clusters in Germany for example, and in other parts of the EU.
It means embracing new ways of doing things, and always questioning: Why? and how?” and trying to improve. Technology adoption and keeping up with the latest industry changes is one thing. But taking it a step further to cultural change also means engaging with the collective whole who are also adapting and learn the best way to do so. The only way to do that is through networks that facilitate knowledge exchanges, with comparison of trial and error to our own business models; the sharing of best practices. This will also change our industry culture.
It also means viewing suppliers as partners and subject matter experts that support your manufacturing operations, in addition to the value and savings your relationships may provide, rather than an adversary trying to gouge you.
My final opening question asks: What are the benefits and why should we bother?
Peer networks are powerful. Imagine how more productive you and your staff would be if you always had immediate answers to burning questions and problems that face you everyday, in the day-to-day aspects of various parts of your operations. This happens constantly. While writing this, my phone alert went off from the WMCO WhatsApp Manufacturers Only chat group where someone was reviewing their pricing methods and wanted to know what others were doing with pricing installations as percentage of job cost.
Another recent example was related to digital integrations projects and the types of investments they were making and why. These are examples of benefits of being linked to a network of other manufacturers in real time; via cluster networks. This is also creating a new culture in our industry; one of open collaboration. Without managed and facilitated networks, whose job it is to facilitate this kind of activity, it would never happen on this scale. To engage this kind of activity, you only need to put your needs out there, and reap the rewards.
Recently, WMCO was successful in obtaining $2.85 million from FedDev Ontario for Digital integration projects to achieve Industry 4.0. WMCO’s last three networking events provided a forum for companies to share their digital integration project challenges and successes. Members also forge new relationships in different ways with people and companies they may not have done before: facilitating “industry culture change”. These types of projects are the trademark of cluster ecosystems.
A final point on the importance of the cultural revolution in our industry is the most important: we are one of the last countries to embrace collaboration for our industry. We are still behind, but getting better. While this is not necessarily our personal fault as individuals, it is up to you and all of us to recognize that if we are to become globally competitive and domestically sustainable in our industry, we all need to participate in the collaborative cultural change this article addresses. The EU has been doing it for 30+ years.
Already, WMCO has many wood manufacturing companies in Ontario leading the charge in culture change for our industry. The WMCO board of directors has ten manufacturing members and three associate supplier members guiding the way.
Become part of the wood industry cultural revolution of change that is moving forward. Many events are open to non-members to sample the experience firsthand.
For more information on WMCO, visit our website at
www.wmco.ca