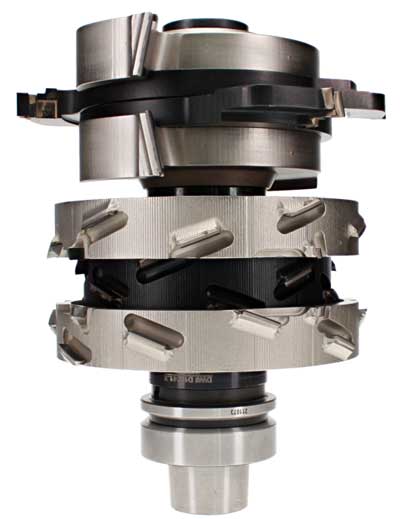
As high shear diamond tooling has evolved many tool manufacturers throughout North America and Europe have been exploring different ways to employ this tool geometry in new applications. For the past decade, much of the focus has been on edge machining applications on solid wood and wood composites. Tool manufacturers have successfully optimized
edge-machining operations on many CNC routers and tenoners, but high shear geometry does have limitations.
High shear diamond geometry is extremely effective at machining straight edge parts or minor angles. However, complex profiles and radius profiles cannot successfully be machined with high shear. As wood products designs have transitions to more contemporary styles, straight edges have replaced complex profiles. Therefore, high shear tooling solutions have become far more prominent in applications where cross grain tear out is problematic. Door edge production has been dramatically improved with
high shear cutting tools, and now a new opportunity has emerged on specific areas
of the tenon joinery.
Traditionally, tenon components have been the most difficult wood part to machine without grain tear out. Tenon components are normally positioned with cross grain orientation and deeper depths of cut are required in many cases, which can be challenging. Machine design and material variations also make this application difficult to perform with a high level of consistency. Many machinery designs have implemented multi rotational heads or “jump heads,” which effectively eliminate blow out but cost of machinery is higher and set up can be tedious.
Image 1 shows a diamond high shear tool designed to produce tenon joinery with high accuracy and premium cut quality. This specific tool is designed for entry door production, but it can be scaled down to produce cabinet door or furniture parts. This tool format is stacked to include groove tool and tenon tool on one arbor to further improve machine efficiency and effectiveness. Notice the high shear angle of the cutting edges on bottom tenon tool compared to the groover design on top of the assembly. Groover tools generally do not require high shear geometry as machining is done with the grain, as opposed to tenons which are always cross grain orientation.
Why is high shear geometry necessary
to machine tendons?
Effectively machining tenons has always been a challenging application for machine builders. A wide range of wood species at different moisture contents, which need to be accurately cut into a wide variety of profile configurations, can be a difficult task. Originally machinery designers built “backer blocks” into the machine design, to reduce blow out. This design is still used in many machine configurations today; however, the backer block approach can be tedious especially if many profiles have to be cut on the same machine. The emergence of tenon machining on CNC routers added new complexities, as backer blocks are not a viable option on CNC routers. There are a variety of ways to improve cut quality on a CNC router by adjusting machine parameters and tool geometry, however, multirotational tooling and programming was the only one hundred percent effective approach, until high shear tool geometry immerged. Most single and double end tenoning machinery is available with multi rotational configurations, which are very effective, but the complexity of machinery does increase cost for machinery and tooling.
High shear cutting tool geometry has emerged as the preferred option for specific profiles for a variety of reasons. Unbeatable cut quality results are the key benefit, which dramatically reduces part defects or required finishing after cutting operations. Tool longevity is another important benefit as high shear geometry has proven to last four to five times longer than traditional diamond tooling and cutting edges tend to be more durable. A large part of the excitement surrounding high shear tools is the simplicity of programming and final operation. The machine programmer simply sets up a single pass in one rotation across the end of part and the high shear cutting edges do the rest. As the tool nears the edge of part, the extreme high shear angles compress material toward the tenon to avoid grain tear out or excessive blow out on the top and bottom edges of parts.
Challenges
High shear tool geometry was originally designed for finishing applications at minimal depth of cut. Most perimeter edge cutting operations are performed at 1/16 to ¼ inch depth of cut depending on material thickness and wood species. High shear angles are extremely effective at eliminating grain tear out, but excessive depth of cuts can load up cutting edges, resulting in heat generation, as chips cannot be extracted efficiently. Some test results, at extremely high feed rates showed chips plugging up the cutting tool causing vibration and poor cut quality. However, these types of tests were performed at ¾ to one-inch depth of cut at high feed rate. Most tenon cutting operations in the cabinet and entry door industry are done at ½ to 5/8 depth of cut, which tends to work much better for high shear tool formats.
Although molder machinery generally runs at feed rates of 60 to 300 feet per minute, tenon equipment tends to run much slower at 20 to 80 ft per minute, which allows high shear flute designs to clear out chips before they plug up cutting tool. Furthermore, tenon components are always narrow compared to long grain components; so high shear tools are cut at full depth of cut for a shorter period. This allows the tool to clear chips effectively as cutting edges are not constantly engaged deep in the cut.
High shear cutting tools can be designed to machine straight edges and a variety of angle profiles; however, radius profiles and other complex profile designs cannot be achieved with high shear geometry. Contemporary profile designs normally have straight or slightly angled features, so high shear tools are well suited to machining modern contemporary profiles, which are most popular in the market today. Furthermore, most problematic grain tear out occurs on straight edges or corners of profiles, so high shear tenon tool designs do address many of the cut quality issues associated with tenon machining.
Conclusion
High shear cutting edge geometry can optimize machine and tool performance in many applications, but its effectiveness is particularly beneficial in tenoning applications. CNC routers and most single and double-end tenoner equipment can be outfitted with high shear cutting tools to optimize machine performance and dramatically improve cut quality. Although high shear tools designs do have some limitations with regards to complex profiles, the solid wood door and furniture industries have transitioned to for more straight edge contemporary profiles, which are easily machined with high shear tooling.