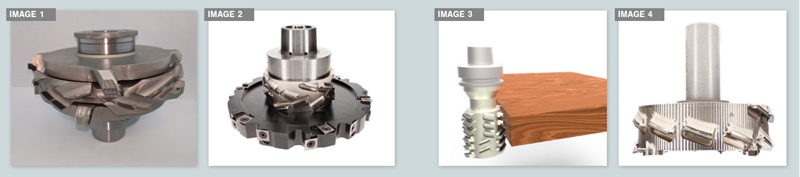
High shear diamond tooling designs continue to advance into new applications to optimize machinery performance and improve cut quality. Most cutting tool manufacturers in North America have started to produce high shear diamond tools in various formats, which have improved machining operations in specific areas. New hybrid tool designs have now emerged to provide greater flexibility and versatility so high shear tools can be used on more material types in new applications. High shear diamond tooling has been proven to improve cutting efficiency and cut quality in many applications using a variety of wood species and composite material. Solid wood doors, furniture and flooring components have been improved by utilizing high shear cutting geometry. Most of these applications involve machining the edge of components with straight profiles, but new rebating
and profiling options have been developed.
High shear benefits: 1) Premium cut quality by eliminating cross grain tear-out
2) Dramatically increased feed rates without sacrificing quality
3) Significantly extends tool longevity and durability.
Why are new hybrid tools required? Geometry limitationsHigh shear geometry can be utilized in straight edge machining and minor angles, but it does have limitations with deeper, more complex profiles. Therefore, tool assemblies must be designed with separate high shear sections and profile sections in one tool stack.
Image 1 shows a tool with high shear geometry in the middle of tool between two sections of traditional diamond tool geometry. This allows the high shear cutting edge to eliminate the grain tearing in the most critical edge of part and still provide profiling in one single pass.
Material compositionsHigh shear tooling products do offer substantial long-term value by reducing tooling cost and improving cut quality. However, there are some materials, which are more likely to damage the diamond cutting edge, which must be avoided to realize the value of diamond high shear tooling. Given the amount of hybrid sandwich materials on the market, it is important to consider where high shear tools are being used. Most natural wood species and wood composites are a good match for diamond high shear, but particleboard and many cement board products contain foreign materials, which will fracture the diamond cutting edge. In this case it is possible to design the tool stack in hybrid format using diamond and carbide cutting edges, with the appropriate cutting edge machining the appropriate material in specific parts of the profile.
Image 2 shows a tool with high shear geometry on the bottom of the tool and a carbide inset tool on top. In this case, the location of grain tear-out was the problem, which needs to be addressed by implementing high shear in one specific area of the tool.
Integrated tool
holder designsUnfortunately, not all high shear tools can be made in an integrated style design for various reasons. As discussed, high shear tools can be designed for straight edges or angled parts of profiles, so assembly of multiple cutters is a very common requirement. This presents a challenge when you look at the specific design of tool in image 1. The high shear section must be separate from the profile sections, which makes it impossible to design a completely integrated style of tool. In order to service and sharpen these diamond tools, they must be disassembled
and sharpened separately to maintain profile consistency and prevent collisions in the sharpening process.
However, there is still an extremely accurate way to design hybrid high shear tools with a hydraulic arbor assembly method. ETP Sweden manufactures a variety of hydro arbors, which effectively eliminate tolerance between arbor and cutting tool by employing their patented GE 2 hydro expansion arbor. The blue cap on bottom of the tool makes it clear an ETP arbor is being used to hold all parts of the assembly securely once pressurized. A simple Allen key can be used to pressurize the tools accurately on the shaft, which results in the least amount of run out. Consistency of sharpening can also be maintained if tools are serviced on the holder and reassembled in the exact same orientation. Although these hybrid assemblies cannot be made in a completely integrated style, the hydro arbor feature does provide the absolute best machine and tool performance possible for tool assemblies.
Whenever possible, integrated tool holder designs are used to ensure maximum balance, rigidity and consistency. Straight edge tools are now becoming very common as tool manufacturers find common tools sizes to stock for popular applications in the industry. Image 3 shows an example of an integrated HSK63F high shear tool for thick wood components. This same design can be modified to include angles up to five degrees, which is very handy for the entry door industry as many doors have three-degree angle dimensions. This allows entry door edges to be completely machined using high shear geometry, even with a 3-axis CNC. If 5-axis CNC is being used, the high shear tool in image 3 can be used for both operations to achieve optimal cut quality on all edges of the door.
Rebate applicationsTool in image 4 shows a high shear tool designed for rebate operations. Notice the spurs on the bottom of tool, which score the material and the wings shearing toward the spurs to provide the best possible cut quality. However it is important to note there are some limitations in this design and it must be used in the appropriate depth of cut and machine parameters. Due to the design of high shear geometry, it is not well suited to for deep depths of cuts, which are common in rebate applications. This tool can be programmed to machine ½ depth of cut per pass or a pre-hog tool can be used prior to high shea tool path.
CONCLUSION The positive effects of high shear tooling have been realized on various machinery and applications, as tool manufacturers create new tool designs and discover new ways to apply high shear geometry. This type of tooling does not provide benefits in every application; however, the cycle time benefits and
cut quality improvements are incredible if used in proper applications. High shear designs will continue to evolve as more demanding applications
and materials continue to drive innovation.