There is one thing that has such an impact on your output and bottom line that is so simple, it is not even explicitly listed in the Lean book. But if you do not solve this problem, no other investment in machines will achieve promised benefits. It is so obvious and sounds so simple, but in reality, it is quite a challenge for many of us and I would say almost all companies struggle with this. I call it fit & complete.”
Let us pretend we take a plant tour and because I like the pull-system, and it makes it easier to point out the constraints, we will walk you through the operation against the material flow.
We’ll start with shipping and ask the shipping manager about his on-time shipping performance. “I ship 100 per cent on-time what I have - 100 per cent of the time,” was the somewhat angry answer. Well, I touched a nerve! When analysing an operation, you look for the following elements:
Information
Equipment
Input material
Established processes
Resources/workers
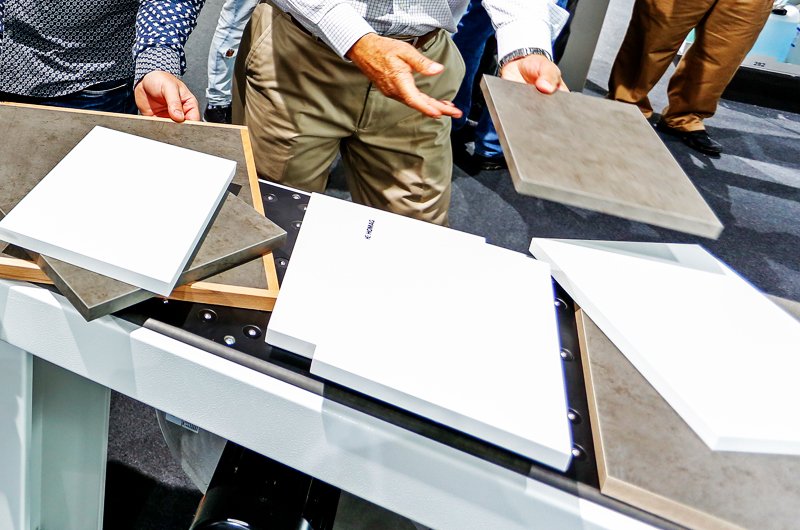
He had the shipping documents, the trucks and the forklifts. He had the workers and they all knew how to do their job, however, he did not have all of the product. And to make it even more frustrating, he had all the product except one unit, which needed to go into the nose of the trailer.
Going further upstream to the assembly area. The department is full of material. With all the WIP buffers full of material, one would expect excellent assembly results and flow. Not so!
Along the assembly line there are incomplete cabinets on the floor. Assemblers are dragging boxes off the line and stacking two-high in the aisles. “We had everything, except the doors which did not arrive from finishing and, because the order is so big, we wanted to get a head start in assembling them.”
Here, again, material was not complete. If one of the pieces required is missing, you cannot complete the product. I will not argue the point that in some rare cases starting the assembly process without having all pieces is the lesser evil, but as a general rule, it is better to start when everything is confirmed as available. The time wasted in stacking down and lifting up again, repairing the damage done by the extra handling, dealing with the congested assembly area, all add cost and slow down output.
The more we are producing to order, the more important fit & complete becomes. We cannot assume that the parts will be there when we need them, we need to confirm it. This can be done by counting and checking manually and flagging the order/unit as available for assembly, or support this function with available manufacturing execution systems (MES) for example WEB-CAB or similar. To simplify the explanation, this type of software will keep track of what is complete and what is not, and gives the signal to allow the next step.
Because companies find it so difficult to coordinate material flow coming from finishing with the flow of the parts that don’t require lacquering, they build days of safety buffers into the material flow. These safety buffers extend lead time, require space, and delay the identification of problems. For example, in kitchen cabinets, I often see the finished fronts get a certain number of days head start on the unfinished parts. This happens with the hope that both parts will arrive at the same time at the assembly area. In todays kitchen cabinet manufacturing environment, with a make-to-order/nesting manufacturing model, we can produce parts within hours (or less) from nesting to assembly buffer. If we can manage the process, we receive the finished fronts (from finishing/supplier), quality check them and then give the signal to the nesting machine to produce the parts.
This leaves relatively few (finished) items/parts waiting for the bulkier case parts.
The next challenge to overcome is fit. We could have all the parts on paper, but they might not fit together. This is a completely different challenge. With product engineering software and direct links to CNC machines, these problems have been reduced, but they are still popping up in manufacturing. The engineering of specials competently is important. Anytime such a mishap hits the shopfloor, assembly gets delayed.
It is not always an engineering error, it can be a manufacturing error as well. Machines, if not monitored, can run out of calibration and wrong adjustments of machines or a damaged part can create a not-fit situation.
I am realistic enough to know that we cannot prevent 100 per cent of all mishaps in a production environment. These interruptions cost much more than the single piece that you have to repair or replace. The interruption to the flow is the real cost. If however, you focus on cutting your error rate through continuous improvement you will drive up your productivity.
As we continue our tour, we ask what is preventing production from being on-time, accurate and complete. What pain points are there, for example, in the machining area? What issues do they have? The most common issue I hear is that they are behind schedule, but they have not received the work orders, cutting/nesting plans or other CNC programs. Another challenge is that the material is not available. These are all examples of not complete input material and information for the task at hand.
This is not the end of the tour. Next we visit engineering and order processing. When pulling and asking why are we not getting more orders to the shopfloor, we will hear a litany of reasons such as, “We do not get all the information we need from sales or by extension from the customers.” Another challenge I often see has to do with weekly batches of assigning the promised ship date. Instead of missing the weekly cut-off, order-entry/sales (knowingly) submit incomplete /incorrect orders, and then issues corrections in the following days. This is an abuse of a system and management needs to recognize and stop it.
The challenge is that in an integrated and automated manufacturing plant, the entire order needs to be specified. With short manufacturing lead-times, as soon an order hits the floor, changes and additions cause major delays.
Customers often have difficulties deciding on, for example, the finish or the handle type and the handle location. Whereas in the old days, there was time to feed that information much later, now it is required to place an order.
Take a look at your operation and check how much time and effort is required on a daily basis to chase missing information and missing parts. And imagine how much easier and more productive work will be when the job arrives at your workplace - both office and shop floor - fit & complete.
It has a ripple effect throughout the organization. Improving fit & complete has a productivity improvement potential of 20 per cent and more, depending on the current situation. It is by far the most significant reason for low performance. Other improvement projects such as faster and more productive equipment might not result in the expected outcome if the company has difficulties achieving sustainable fit & complete. There are many symptoms for out-of-control fit & complete.
Reduced outputOne of the largest impacts is reduced output. You don’t seem to reach anywhere close to the calculated capacity. Another symptom is uneven output. There are big differences from one day to the next. Typically the schedule is not met.
Material buffers are fullThe factory floor is overloaded with WIP and there is no flow in the assembly area. The upstream operations lose time as they have difficulty finding space for the material, whereas downstream is losing time looking for the right material.
Interrupted assemblyAnother sign of incomplete and not fit is partially completed product taken off the assembly line.
Frustrated workersAs workers need to look for information or components, starting processes and then switching over will not allow them to achieve their day’s work. This type of situation leads to frustration and tension. Employees might quit for lack of job satisfaction or worse, they stay, but have checked out emotionally. Successful daily work is a big motivator.
False bottlenecksRecognizing shortages and rectifying them requires fast reaction time. A system of expedited correction needs to be implemented. Certain processes cannot handle these interruptions well and will be identified as bottlenecks. The machines have sufficient capacity however, now we feel the need to buy an extra machine to fix this bottleneck. If done correctly the first time, there would be no need for extra equipment.
Late ordersIncomplete and misfit parts/components lead to late orders and disappointed customers. This impacts the company reputation and will lead to reduced sales. Companies might not yet have a negative impact on sales because their competitors have the same problem. Imagine if your competitors get it right and provide 100 per cent on-time and complete orders and you have not improved. How long will it take to impact your business?
Extended lead timeTo counter incomplete and misfit parts, companies will build in extra lead (safety) time. If incomplete and misfits happen too often, certain workplaces build in time to allow time to correct the situation. If all parts arrive fit & complete all the time, you no longer need waiting time before the next operation. If all parts arrive fit & complete 98 per cent of the time, you might maintain the process with some effective expediting. If fit & complete is only achieved 70 – 90 per cent of the time, your process-flow collapses and you often need to build in a few days to achieve fit & complete. Now, with more days of WIP on the shop floor, we need more space and more time to find the right space. Long lead time on the shop floor leads to other side effects leading to other waste.
How to improveFirst, you need to understand and quantify what is holding up your process. Is it because of fit & complete? Where is the hold-up? Once you understand the reason(s), you can develop corrective actions as a second step.
ExpeditingHaving a dedicated person drive the fit & complete process is an immediate step. Expediting is a double-edged sword. If everybody does their job correctly, you would not need expediting. If expediting is getting the job done, then the organization will become dependent on the expediting function and stop improving because they rely on this safety net. Management must not accept expediting as a permanent fix. It must challenge the organization not to rely on the expediting function. To start this improvement process, the expediter’s insight is invaluable for your corrective action plans. Eventually a proper schedule must replace the expediter.
Capital investmentNew machines will improve the processes, however, they are, in many cases, not the most effective solution. Of course, if the old equipment is producing out of tolerance and requiring constant rework, the justification for new equipment is easily made. Also, the switch from cutting and drilling to nesting usually improves tolerances (improves fit) and reduces looking for parts (smaller batch-size improves complete).
New softwareIn many cases, effective software will improve conveying the required information to the right person/place. Software is a long-term solution but does not solve the underlying problem.
DisciplineThe biggest impact, by far, is usually when everyone in the process chain does their job correctly and consistently. This is easier said than done, but there is no real alternative to doing it right – the first time and all the time. If you can recognize certain errors or omissions that occur repeatedly, analyze them and find an improvement to minimize reoccurrences. Often the processes are not fully defined. Documented processes simplify retraining.
The fact that this is a common problem in our industry, the promise of huge productivity improvement potential, makes this one of the most rewarding projects.
Also, the fact that a bad performance on fit & complete diminishes the benefits of any other improvement project, makes it even clearer that we must start here.
The objective and the process sound obvious and even simple, but the implementation is not easy and takes focused work. It is worth the effort!