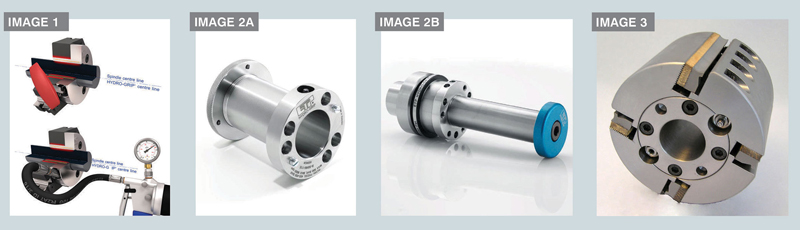
Hydraulic tool holding systems are an extremely effective and practical investment to help optimize the performance of cutting tools and machinery. Hydro-lock technology was brought to market by ETP Transmissions in the 1980s, and they have continued to develop their technology in conjunction with tooling and machinery innovations. ETP hydraulic clamping technology can be used by any tooling manufacturer to improve tool connection to most woodworking machinery.
THE HYDRAULIC ETP PRINCIPLE:
The scientist Blaise Pascal formulated the principle of pressure propagation in liquids many years ago:
“A liquid confined in a vessel which is subjected to pressure distributes the pressure uniformly upon the walls of the vessel.”
Image 1: shows this principle at work in an ETP hydro sleeve cross section.
All ETP products consist of a double-walled hardened steel sleeve, filled with a pressure medium (usually grease). In the flange there are one or more screws and a piston with seals for the pressure setting. All work according to the hydraulic principle: when tightening the screw an even and moderately high surface pressure is created against shaft and hub. Early hydraulic clamping systems focussed on large cutting tools for moulders, but more recently ETP has focussed on CNC router and CNC moulder mounting systems. All products are designed with the same concept which leads to the following advantages.
Benefits:
• Safe accurate mounting of tooling to machine spindle or interface
• Provides minimal tool run out resulting in premium surface finish
• Allows machine to operate at higher feed rates & RPM without sacrificing finish quality
• Quick convenient tool changes
Hydro Sleeves
Image 2A: shows a traditional hydro sleeve, which is mounted into cutting tools to serve as an accurate connection point to the machine spindle. The grease pressure in this case can be applied through use of an external grease gun, or alternatively self contained ETP products require only an Allen wrench to tighten an actuator screw, which drives grease pressure into the chamber and clamps the cutting tool without any external grease.
Hydro arbors
Image 2B: shows a very useful holding system for CNC router, moulder or shaper tooling. The unique part of this product is the expansion of the arbor instead of the expansion of the sleeve onto an arbor. This is achieved with the same ETP technology built into the walls of the arbor, which will expand outward by simply turning an Allen screw, which pushes an actuator to expand the walls of the arbor and clamps the tool onto the arbor accurately and safely. This system is the absolute best way to mount cutting tools onto spindles for higher RPM applications, particularly on CNC routers. There has been a dramatic market shift to larger, more complex tooling designs being mounted on CNC routers for extremely demanding applications.
For example, large tool stacks for window production or entry doors are often very complex tool designs which required accurate set up and tool balance. The ETP hydro arbor is a critical component, which not only allows the tool to be installed initially, but also allows technicians to disassemble tooling and re-assemble quickly and accurately. This function becomes very useful with tooling assemblies that require groove size adjustment by removing tool from arbor. ETP hydro arbors provide the safest way to install tooling and maintain critical balance for higher RPM CNC machines.
Hydro arbors are available for high RPM CNC power lock moulders to promote safe operation and optimal machine performance. Machinery running at 4,000 to 7,000 RPM can afford to have moderate inaccuracy in tool balance with minimal risk, however, 8,000 to 12,000 RPM machines cannot be run with the same margin of error, and ETP hydro arbors can reduce the margin of error substantially.
Integrated hydro sleeves
ETP Sweden has dominated the market for hydraulic units, separate from the cutting tool, and remains the best performing product, despite attempts from offshore copy cats. But there is an alternative in some cases when an ETP hydro sleeve is not an option. Some tool manufacturers in North America have the capability to produce ‘integrated’ hydraulic systems, which are manufactured as part of the cutting tool and cannot be removed. This option is only available in large cutting head formats, but can be a very effective way to hold large moulder heads when a separate ETP sleeve is not available. The integrated hydro option functions virtually the same as ETP, but must be dedicated to a single tool body.
Image 3: shows and integrated hydro sleeve built into a corrugated head.
Hydraulic clamping is not new technology, but it has served as a critical difference for many years in tooling and machine installations. Traditional hydro sleeves have evolved into CNC router products, which continue to provide optimal machine performance and safety throughout the industry. When considering new tooling designs, always consider quality of tooling holding options, before deciding on tool configuration. Your tooling and machine are only as good as the clamping system which connects them.